Austin Hayes paves the way: creating new standards in health and safety using science and an XRF analyser
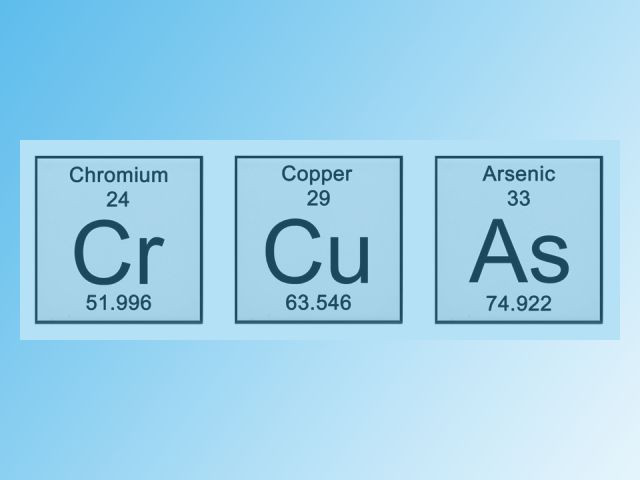
Austin Hayes has broken new ground yet again. With the help of Peritus Health Management and top-of-the-range XRF analyser, we’ve created new health and safety protocols that will help our staff to process contaminated materials, such as ammunition boxes treated with Chromium Copper Arsenate (CCA), in an efficient and risk-free way.
How it all started
When it comes to the health and safety of our team, Austin Hayes doesn’t compromise. From operating heavy machinery to handling a variety of materials and transporting goods around the factory floor, our employees adhere to strict guidelines to ensure that they’re always protected.
Usually, this is just a matter of following long-established company protocols. However, when we were asked to undertake a challenge we’d never encountered before – recycling ammunition boxes that were contaminated with the harmful substances CCA – we discovered that there were no existing health guidelines to help us through the process. We knew, though, that this was a task that we needed to take very seriously.
Identifying the problem
The dangers of handling the hazardous substances found in the wooden boxes were of primary concern. Chromium, Copper and Arsenate can each cause a range of acute and chronic health effects, and can enter the body through inhalation, ingestion and/or absorption. These substances can create problems with the respiratory system and cause neurological damage, cardiac symptoms and even cancer. Simply put, CCA can be deadly, and every attempt should be made to reduce exposure to a minimum.
Assessing the threat
Our first step was to find out exactly how contaminated the wood really was. To help us achieve this as precisely and reliably as possible, we invested in a state-of-the-art XRF analyser, which could calculate extremely specific readings on the levels of different substances within the wood. Complementing this investment, two members of Austin Hayes’ management team also undertook an intensive radiation awareness and RPS course, learning everything there was to know about conducting this part of the process safely and effectively.

Everything was in place to help us see what we were dealing with. Now, all we needed to do was find out the best possible way to dispose of the contaminated wood safely. It was obvious that we couldn’t follow the same health protocols that we had before. We would have to create a new system from scratch, factoring in the potential dangers of handling the contaminated wood and how CCA could affect the disposal process.
This wouldn’t turn out to be easy. When we started doing research, we found that there was nothing to go on – no records of companies that had attempted this before, no white papers which illustrated the best practices to follow, or really anything useful that we could base our approach on.
Taking matters into our own hands
We partnered up with Peritus Health Management – a company that specialises in occupational health and hygiene – to help us determine what safety measures we would need to take. Together, we decided to undergo some experiments that would identify all of the potential risks of handling the contaminated wooden boxes, and depending on the results of these experiments, would draw up a list of safety guidelines for the team at Austin Hayes to follow.
Extensive research
Of course, as this type of procedure hadn’t been done before (at least in a scientifically recorded fashion) we had to get creative. To achieve the most accurate results possible, Peritus used a familiar methodology – surface wipe sampling – which is used to examine the levels of lead in surface dust. In our experiment, we attempted to replicate the various ways an Austin Hayes employee might touch the contaminated wood, to illustrate how this could affect the possible transference of CCA.
After repeating the test to ensure the experiment was reliable, we ascertained that CCA could be transferred onto the skin when handling the wood. This was because it had previously been applied as a liquid and then absorbed into the wood. The risk of exposure, then, was likely to be caused by dried CCA particles getting onto the hands, and then being theoretically inhaled, ingested or absorbed into the body, posing a risk to workers’ health.
Laying the foundations
Due to the dangers involved, it was crucial that a standard operating procedure was developed and strictly adhered to by employees. Furthermore, all employees who would handle the contaminated wood were to receive the required training beforehand, in which they would be observed for competency.
Regular biological monitoring was also deemed necessary to evaluate control measures. The working environment would need to be monitored regularly, and health surveillance was to be carried out based on the findings of the tests. Due to the associated risk, we agreed that these new CCA specific health records should also be kept for all employees by Austin Hayes for 40 years.
Finally, new procedures for how to use personal protective equipment (PPE) were introduced, such as how to safely dispose of the single-use Nitrile gloves that employees must wear when handling the contaminated wood.
Winning results
By investing in an XRF analyser, working with Peritus and training all of our staff accordingly, new opportunities have presented themselves for the entire team at Austin Hayes. Exploring this uncharted territory has positioned us as a company that’s now uniquely capable of interacting with and identifying contaminated materials, so that they can be handled and disposed of safely. With the help of Peritus’ expert insights, ongoing support and meticulous attention to detail, we’re confident that our work in this field will be extremely valuable to us and our partners in the years to come.